The Function of Foam Control in Enhancing Product High Quality and Efficiency
Foam control is an often-overlooked yet important part in the pursuit of item high quality and functional performance across diverse industries. By effectively managing foam formation, firms can not only boost the consistency of their formulas however additionally tackle functional obstacles that can hamper productivity. This discussion will certainly explore the multifaceted impact of foam on both item integrity and manufacturing processes, increasing vital concerns concerning the methods that can be used to enhance foam control. As we consider these implications, it ends up being clear that the risks are greater than they may at first show up.
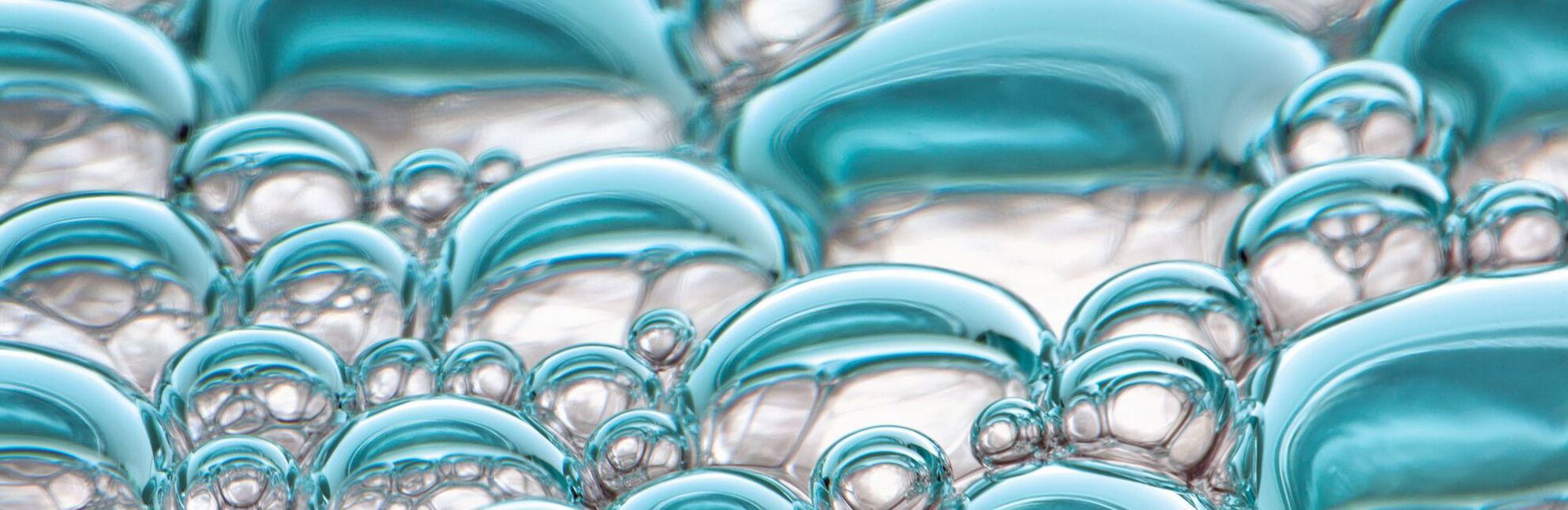
Comprehending Foam Formation
Foam formation is a complicated sensation that can substantially affect product quality and functional performance throughout numerous industries. It takes place when gas bubbles come to be trapped in a liquid, leading to the creation of a foamy structure. Numerous variables add to this procedure, consisting of the chemical and physical residential or commercial properties of the fluid, the visibility of surfactants, and the problems under which mixing takes place. Understanding these variables is important for managing foam efficiently.
The liquid's thickness and surface area tension play critical duties in foam stability. Surfactants, for example, can minimize surface stress, promoting bubble development however additionally improving foam stability, which can be troublesome in particular applications. In addition, mechanical anxiety, temperature level changes, and the presence of contaminations can exacerbate foam generation, making it important to keep track of these facets throughout manufacturing procedures.
Industries such as food and beverage, pharmaceuticals, and chemical production have to be particularly attentive regarding foam control. By grasping the hidden systems of foam development, organizations can carry out targeted techniques to minimize its results, thereby protecting operational efficiency and making certain consistent product performance.
Influence on Product Quality
The presence of foam can significantly endanger product high quality throughout numerous markets. In manufacturing processes such as food and drink, drugs, and cosmetics, excessive foam can bring about inconsistent product solutions. As an example, in food manufacturing, foam may catch air, affecting texture and taste, which can ultimately alter customer perception and contentment.
Furthermore, foam can impede the uniformity of coverings and paints, resulting in flaws like bubbles and irregular coatings. In pharmaceutical applications, foam can hinder the accurate application of liquid medicines, possibly impacting therapeutic efficacy and client safety. These high quality issues not just reduce the end item's charm yet can likewise bring about pricey recalls and damage to brand name credibility.
Furthermore, the presence of foam can complicate quality control actions, making it hard to accomplish consistent outcomes and precise measurements. Effective foam control not only minimizes these threats but also enhances overall item quality by making sure that formulas fulfill stringent industry requirements. By spending in foam control methods, companies can secure their products, boost consumer satisfaction, and preserve an one-upmanship in the market.
Operational Difficulties From Foam
Effective operations in various markets can be severely interfered with by the presence of foam, which presents numerous difficulties throughout manufacturing procedures. Foam can hinder mixing and response times, hindering the performance of chemical procedures. In industries such as food and beverage, foam development can result in inaccurate fill degrees, causing item waste and inconsistencies in packaging.

In environments where view it now hygiene is critical, such as pharmaceuticals and food processing, foam can complicate cleansing procedures, creating covert reservoirs for pollutants. This not just increases quality problems however additionally can bring about compliance concerns with regulative standards.
Additionally, the psychological influence on drivers can not be forgotten; too much foam can create a chaotic job environment, causing decreased spirits and productivity. In summary, attending to the functional difficulties positioned by foam is crucial to preserving efficiency and item quality in pop over to these guys different sectors.
Techniques for Reliable Foam Control
Just how can sectors effectively minimize the difficulties posed by foam? Reliable foam control techniques are necessary for boosting product quality and operational effectiveness.
In addition to chemical remedies, process optimization plays a vital duty in foam monitoring. Industries can assess and change specifications such as blending rate, temperature, and pressure to reduce foam generation. Carrying out tools alterations, like installing foam-breaking tools or adjusting tank layout, can better help lower foam degrees.
Routine monitoring and analysis of foam behavior within manufacturing procedures are additionally important. Using sophisticated sensors and analytics can give real-time data, permitting for timely treatments and adjustments. Team training is equally crucial; making certain that employees are educated regarding foam dynamics and control strategies can result in aggressive foam management.
Situation Researches and Industry Applications
While lots of industries face distinct difficulties associated with foam control, study expose that tailored strategies can dramatically improve both item high quality and operational effectiveness. In the pharmaceutical sector, for example, a leading producer executed a personalized foam control technique that reduced foam development during Visit Your URL fermentation processes. This innovation not just improved yield by 15% however likewise reduced contamination risks, making sure higher item integrity.
Similarly, in the food and beverage industry, a major dairy products producer confronted excessive foam throughout pasteurization - Foam Control. By introducing a specialized antifoam representative, they reduced handling time by 20%, which directly equated to enhanced throughput and reduced energy usage. The application of foam control measures ensured constant product structure and taste, reinforcing brand commitment
In the chemical manufacturing field, a study highlighted the successful application of foam control in wastewater therapy processes. The implementation of a real-time surveillance system allowed drivers to adjust antifoam dosage dynamically, leading to a 30% reduction in chemical use and improved effluent top quality.
These study show the varied applications of foam control throughout markets, highlighting its vital role in boosting product top quality and operational performance.
Verdict
In conclusion, effective foam control is essential to enhancing product quality and functional performance throughout numerous markets. Eventually, prioritizing foam control contributes to improved productivity, guarding brand track record, and boosting client complete satisfaction, highlighting its value in high quality guarantee within producing procedures.
Foam control is an often-overlooked yet essential component in the quest of product high quality and functional performance across diverse sectors. Team training is just as important; ensuring that employees are educated regarding foam dynamics and control methods can lead to aggressive foam monitoring.
While lots of sectors face one-of-a-kind challenges connected to foam control, instance studies expose that tailored strategies can dramatically improve both item quality and operational performance (Foam Control). In the pharmaceutical sector, for instance, a leading manufacturer carried out a customized foam control strategy that decreased foam formation throughout fermentation processes.In final thought, effective foam control is important to enhancing product quality and functional efficiency throughout different sectors